TU Graz develops autonomous electric compost turner
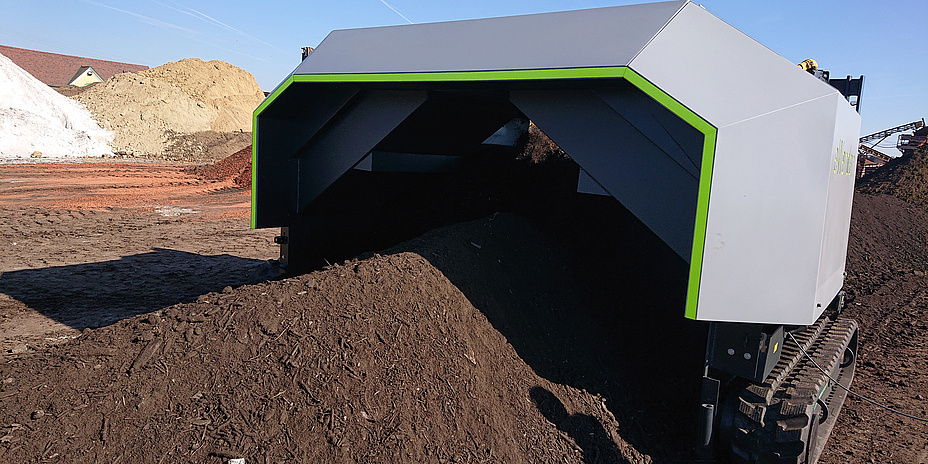
Turning and mixing large compost heaps are important steps in composting to speed up the rotting process. Composting plants and agricultural businesses use mostly tractor-drawn turners or a diesel-powered compost turner with crawler track. The operators of these machines are exposed to extremely unpleasant conditions due to the slow travel speeds (from 50 to 300 m/h), high ambient temperatures, the gases released and the odours that occur during the turning process.
As part of the ANTON (Autonomous navigation for tracked compost turners) research project, researchers from the Institute of Logistics Engineering and the Institute of Geodesy at TU Graz are currently working on an autonomous compost turner that will be able to carry out the turning process without the need for personnel in the future – and in an environmentally friendly manner: The new machine is operated with a battery electric drive concept that has already been successfully tested in preliminary research projects.
Play video
Innovative navigation system
The first innovation lies in the navigation module, as explained by project coordinator Manfred Wieser from the Institute of Geodesy: "In the composting yards, the compost is usually piled up in two-metre high trapeze-shaped lines arranged in several rows. In order for the four-metre wide and two-and-a-half-metre long machine to be able to target these lines and turn the compost correctly, precise positioning is necessary."
The project team at the Institute of Geodesy implemented a navigation system for this purpose, which records the location of the compost turner in real time with centimetre accuracy. High-precision positioning is provided by global navigation satellite systems (GNSS), such as GPS and the European GALILEO system. To increase the robustness and to be able to bridge failures of the satellite signal, accelerometers and angular rate sensors, stereo camera data, sensors on the chain-driven wheels and a highly accurate 3D model of the composting plant are also used. Two GNSS antennas and imaging sensors on the machine itself ensure that the direction of movement is clearly determined.
Robust control architecture
To ensure functional reliability and save development time, the team from the Institute of Logistics Engineering is currently testing the compost turner in a virtual environment rather than at the composting site. For example, the behaviour of the crawler chain on the often and rapidly changing ground at the composting site is simulated, as well as the influence of the different degrees of compost maturity on the turning roller. The results are incorporated into the final development of the control sensor technology and the control structure. "The dynamic description of autonomously driving tracked vehicles in virtual models has so far not been as established as that of autonomous passenger cars. This is where we are doing pioneering work with our research," says Christian Landschützer from the Institute of Logistics Engineering.
The logistics expert underlines the social importance of the research project: "In Austria, we produce over one million tons of organic waste annually, which is processed in over 400 composting plants. Moreover, composting plays a major role in those countries that have a shortage of fertile soil." The interest and demand for an autonomous compost turner is great, and the researchers are already in contact with several companies. The Styrian company Pusch & Schinnerl is the project partner and is preparing the industrial implementation. Wieser and Landschützer hope that the new development will be completed by the end of the year and that a prototype will be ready for production as early as 2021.
Play video
The battery-electric turner should be able to drive autonomously in the future
The ANTON research project is funded in the framework of the Austrian Space Applications Programme (ASAP) of the Austrian Research Promotion Agency FFG and is anchored in the Fields of Expertise "Mobility & Production" and "Sustainable Systems", two of the five strategic research core areas of the University.
Kontakt
Manfred WIESER
Ao.Univ.-Prof. Dipl.-Ing. Dr.techn
TU Graz | Institute of Geodesy
Phone: +43 316 873 6348
manfred.wieser @tugraz.at
Christian LANDSCHÜTZER
Assoc.Prof. Dipl.-Ing. Dr.techn.
TU Graz | Institute of Logistics Engineering
Phone: +43 316 873 7325
landschuetzer @tugraz.at