Wire-Based Additive Manufacturing of Ti-6Al-4V Using Electron Beam Welding
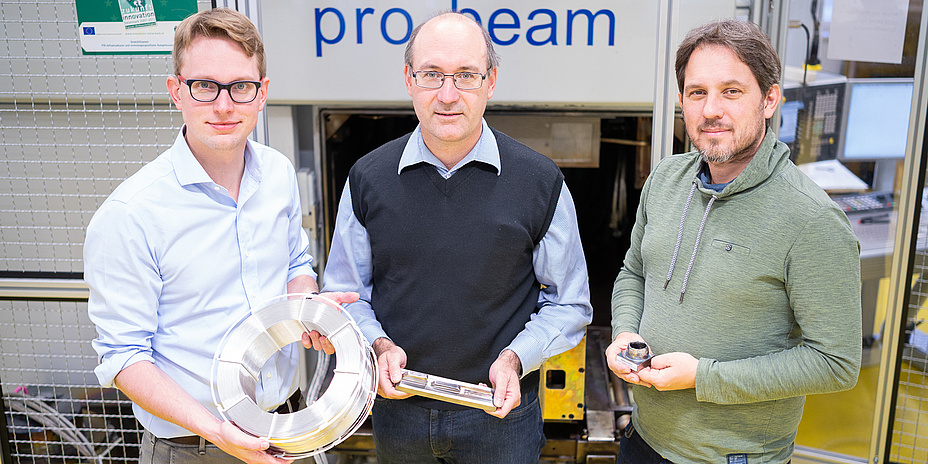
While powder bed processes are widespread and enable the production of very small and complex structures, wire-based processes are less common. However, due to the usability of standard welding wires, a huge variety of different materials are available, and due to the nature of the used arc and electron-beam process characteristics, much higher deposition rates can be achieved and hence bigger structures can be produced.
Electron-beam freeform fabrication is a wire-feed direct energy deposition additive manufacturing process with up to 200 cm³/h using conventional welding consumables to create near net shape parts. The vacuum atmosphere ensures an excellent shielding against atmosphere and enables processing of highly reactive materials like titanium alloys. In current ongoing activities at the Institute of Materials Science, Joining and Forming at TU Graz, electron-beam additive manufacturing (EBAM) technique is applied forthe α-β-titanium alloy Ti-6Al-4V. First, theoptimization of the machine settings for single bead-on-plate are performed usinga Design of Experiments (DoE) approach.
&nbs
Electron beam welding device at the Institute of Material Science, Joining and Forming, TU Graz.
The correlation between dimensions and the dilution of single beads based on selected process parameters, leads to an overlapping distance in the range of 2/3 to 3/4 of the bead width, resulting in a multi-bead layer with a sufficiently uniform height. A layer dependent, continuously reduced power input results in an almost linear build-up rate. Stacking of layers with different numbers of tracks with an alternating symmetric welding sequence allows the manufacturing of simple structures like walls and blocks which are then used for basic mechanical and metallurgical characterisation.
Dilution and geometric evolution of single beads deposited with different parameter configurations in the course of the DoE Investigation
A number of different activities in this field have led to increased knowledge, and can be summarized as follows:
- Exact adjustment of the wire-tip position and monitoring during process is necessary. The standard equipment is currently under a re-design procedure to improve its reliability.
- Dimensions of beads can be adjusted mainly by beam current, welding velocity and wire-feed rate.
- A proper overlapping distance leads to a flat surface of the built structure as a precondition of a sound build up.
- Robust building of blocks with a linear growth rate is possible by a symmetric welding sequence with adjusted parameters.
- A customized heat treatment is developed to meet the special conditions of this process.
- Using a properly developed procedure, even inclined walls can be built.
- Temperature can be measured by the application of a pyrometer which is protected by a specially developed device using a continuously fed shielding.
a) Alternating symmetric welding sequence to build-up rectangular EBAM structures and b) measured accumulated height over number of layers and ascertain growth rate by the means of linear fit.
Microscopy investigations reveal that they primary structure consists of epitaxially grown columnar prior β-grains, with some randomly scattered macro and micro pores. The developed microstructure consists in apparent martensitic structure with a moderate and uniform hardness of 334 HV. Tensile testing of single samples shows a rather low fracture elongation of 4.5 % and an ultimate tensile strength of 953 MPa. A subsequent stress relief heat treatment (PWHT 710°C / 2h) leads to an almost uniform hardness distribution and an improved fracture elongation of 9.5 %, with a decrease of the ultimate strength to 881 MPa due to the fine α-lamellar structure produced during the heat treatment. Charpy impact results show generally a high impact toughness in the “as-deposited” condition compared to alternative AM techniques such as powder-based SLM or EBM. A slight anisotropic behaviour is observed. Furthermore, after the performed PWHT the absorbed energy is reduced and similar to the as-deposited condition a directional dependence can be reported.
SEM micrographs of fractured surfaces of a) “as-deposited” LD-orientation and b) stress relief PWHT TD-orientation Charpy V-notch specimens. Source: TU Graz / IMAT
Due to the prevailing vacuum atmosphere the heat transfer and down cooling of the AM structures takes place by heat conduction and radiation only. With increasing number of layers the boundary conditions change significantly and consequently the interpass temperature will increase. This will lead to changed thermal cycles, and thus different microstructure evolution and related mechanical properties with increasing height of the AM-structure. Due to its changing geometry, conventional contact temperature measurement by means of thermocouples is not suitable and contactless temperature measurement is preferred. Therefore, a commercial pyrometer with a customized protection device was implemented to determine representative thermal cycles and derive the temperature field in electron-beam additive manufacturing.
a) Recorded thermal cycles for selected distances to the electron beam center (10 mm to 35 mm) during electron-beam additive manufacturing; b) Derived temperature distribution described by reconstructed isotherms.
A detailed publication of this ongoing work is planned in near future. Contributions from different individual projects and theses are considered in this short summary:
[1] P. Peter, master thesis „Drahtbasiertes additives Fertigen von Ti6Al4V mittels Elektronenstrahlschweißen“, TU Graz, 2017 („WKO-Forschungsstipendium“ - Scholarship)
[2] J. Fuchs, master thesis „Drahtbasierte additive Fertigung mit dem Elektronenstrahl und einer unlegierten Massivdrahtelektrode“, TU Graz, 2016 („Dobeneck-Technologie-Stiftung“ - Scholarship)
[3] D. Theuermann, master thesis „Integrierte und kontaktlose Temperaturkontrolle beim Elektronenstrahlschweißen“, TU Graz, 2019 (COMET K2 IC-MPPE Project P3.10 AM Tool, „Dobeneck-Technologie-Stiftung“ – Scholarship)
[4] Wischenbart, bachelor thesis „Kalibrierung eines Pyrometers in der Elektronenstrahlschweißanlage für kontinuierliche Temperaturmessung“, TU Graz, 2018 („Dobeneck-Technologie-Stiftung“ - Scholarship)
[5] D. Barisic, master thesis “Improvement of EBW wire feed”, TU Graz, ongoing („Dobeneck-Technologie-Stiftung“ - Scholarship)
[6] F. Pixner, PhD thesis “Wire based Additive Manufacturing of tool components”, TU Graz, ongoing (COMET K2 IC-MPPE Project P3.10 AM Tool)
[7] D. Skuhla (University of Maribor), master thesis “Toughness optimization of EBAM Ti-6Al-4V by appropriate PWHT”, TU Graz and University of Maribor, ongoing (in the frame of a STC project & Erasmus)
[8] M. Sahul (Slovak University of Technology in Bratislava), post-doc activity “Wire based additive manufacturing”, TU Graz, 2019