Turning Grey into Green
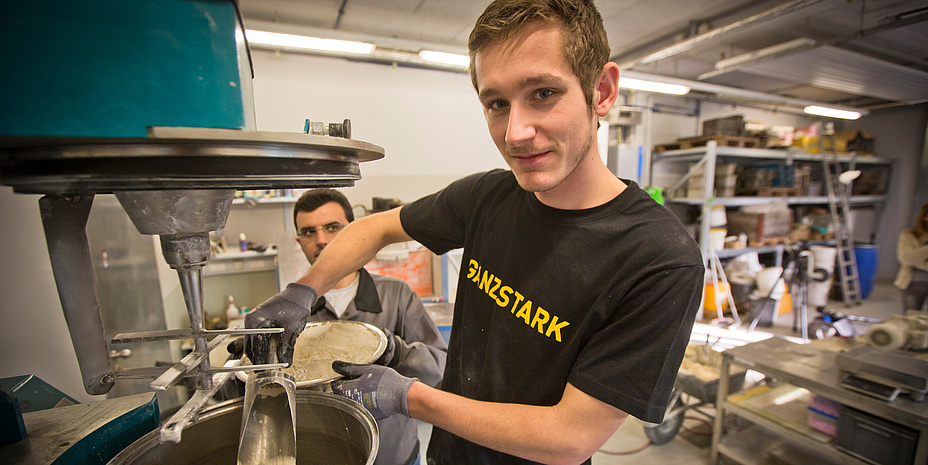
Reduce environmental impact
Is it possible to produce resource-efficient types of concrete using the current wellproven construction techniques and available materials? Following on from this question, Joachim Juhart and the research team at the Institute of Technology and Testing of Construction Materials at Graz University of Technology are researching into different kinds of concretes with less environmental impact. “We want to be able to work with the starting materials available now as well as the well-proven construction techniques in concrete building practice, but we want to reduce the environmental impact of concrete using a more efficient exploitation of resources,” says Juhart, explaining his research approach. It is the cement necessary for the production of concrete – especially Portland cement – that is chiefly responsible for the ecological footprint. Portland cement has to be heated to a temperature of 1450 °C using fossil fuels. At this temperature, limestone, among other raw materials, deacidifies thus releasing CO2.Ultra high-performance concrete
One approach would be to find completely new, environmentally friendlier binding agents instead of Portland cement. International research is being carried out on this. But at Graz University of Technology a more direct way has been chosen of using the materials available today in combination with Portland cement in the production of concrete, while at the same time making use of findings from research into ultra high performance concrete (UHPC). Basically, concrete consists of rock particles graded according to size which are surrounded and bound by finestgrain cement using a binding agent (a mixture of water and a powder which is in turn composed of Portland cement, hydraulic materials and fillers). As a rule, to be able to process the mixture, more water has to be added than is necessary for the chemical reaction. Voids between the particles are thus filled with water and the particles surrounded by a film of water. The water not expended on hardening later causes pores in the hard concrete, in particular capillary pores, which brings disadvantages in terms of hardness and durability. In the case of UHPC, however, the binding agent cement is optimised with respect to its packing density by the addition of microfiller (extremely fine grain) which fills up the voids and even reduces water requirements for a particular degree of workability. Water requirements can be additionally reduced by the addition of solvents. Finally, an extremely hard, tough concrete is produced with a very low water to binding agent ratio.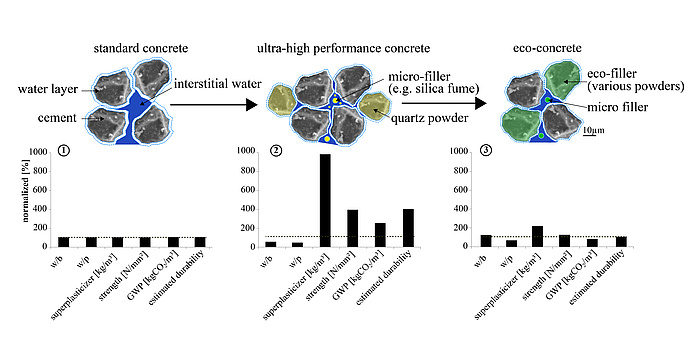
Packing density optimisation and water reduction
This concept is being used for the production of eco-friendlier concrete. Additionally to packing density optimisation and reduction of water requirements by means of micro-filler, part of the cement is replaced by a so-called eco-filler. These materials are regionally available with – compared to Portland cement – reduced global warming potential (GWP) and primary energy consumption (PE). “The big challenge is, first, to identify the right materials, and secondly, to achieve the right mixture ratio,” explains Joachim Juhart. To this end the researchers have developed a new combination of known methods of analysis: MEM-ST (Mixing energy method spread-flow test und strength test). This allows available materials to be classified with regard to water requirements and packing density, and optimally matched to each other. It’s also important to evaluate all the starting materials for concrete with respect to their environmental effects. Only in this way can a mix be found which is optimal regarding both technological performance and eco-friendliness.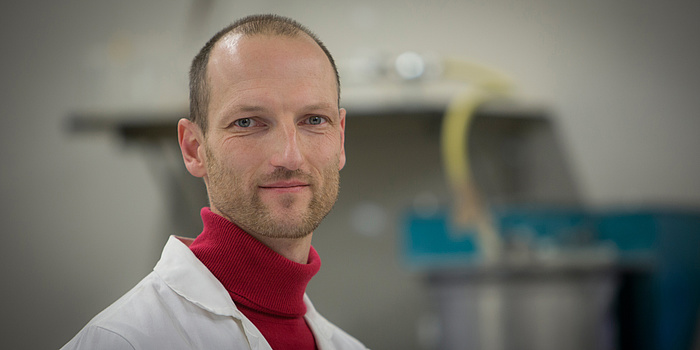
Concrete implementation
Research is currently being carried out in two projects. “Öko²-Beton” was commissioned by the Association of Precast Industry and is particularly oriented to the demands of the precast industry. For example, precast concrete parts have to become hard within eight hours to allow the pieces to be dismantled and lifted. In the second project, “ERESCON”, which was put out to tender by the Ministry for Transport, Innovation and Technology in cooperation with ASFINAG and ÖBB, the focus is on infrastructure construction and thus ready-mixed concrete. Currently, the Graz University of Technology team is translating the laboratory results into real production conditions and would like to build a demonstration element. “This element will show that concrete can be produced using less Portland cement but with supplementary materials, and that it is eco-friendlier, but has the same features or identical performance capacity compared to traditional concrete,” explains Juhart. “We hope, together with our external project partners, subsequently to be able to build prototypical elements or structures,” says Juhart, with an eye on the future. “In any case, we’ve got a good concept for the future development of environmentally friendlier and durable concretes.” Finally, the idea is to support the formulation of new standards which will make the comprehensive use of ecologically improved concrete possible.
Kontakt
Dipl.-Ing. Dr.techn.
Contact person for research in concrete technology
Institute of Technology and Testing of Construction Materials (IMBT-TVFA)
Inffeldgasse 24
8010 Graz, Austria
Phone: +43 316 873 7161
<link int-link-mail window for sending>joachim.juhart@tugraz.at
<link http: www.tvfa.tugraz.at _blank int-link-external external link in new>www.tvfa.tugraz.at