The Digital Revolution in the Workshop
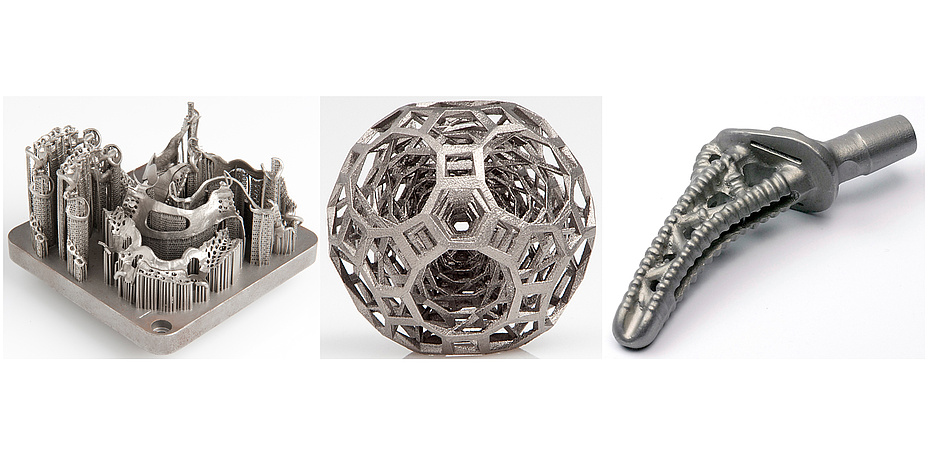
Selective laser melting
In the meantime Additive Manufacturing (better known as 3D printing) is being carried out using all kinds of materials, such as metals, plastics, ceramics, concrete and also biogenic materials. All these technologies require a lot of further investigation and sound research. As one of the core institutes of the Smart Production Initiative the Institute of Production Engineering with its department for Advance Manufacturing will thus acquire selective laser melting equipment for metal printing in order to gain new insights into this modern technology in the wide fields of generative manufacturing.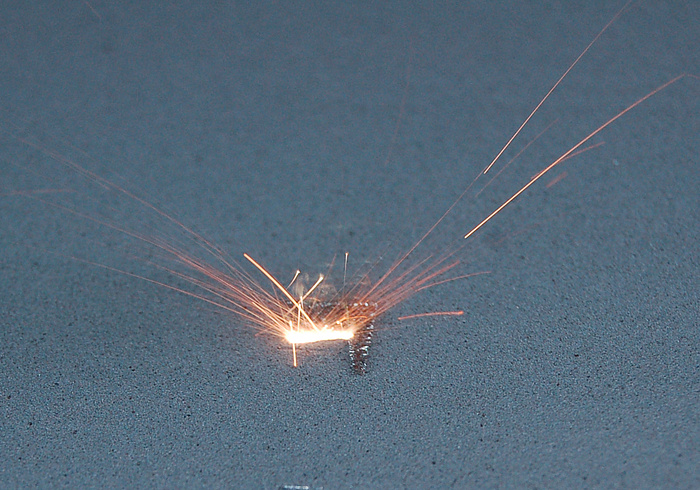
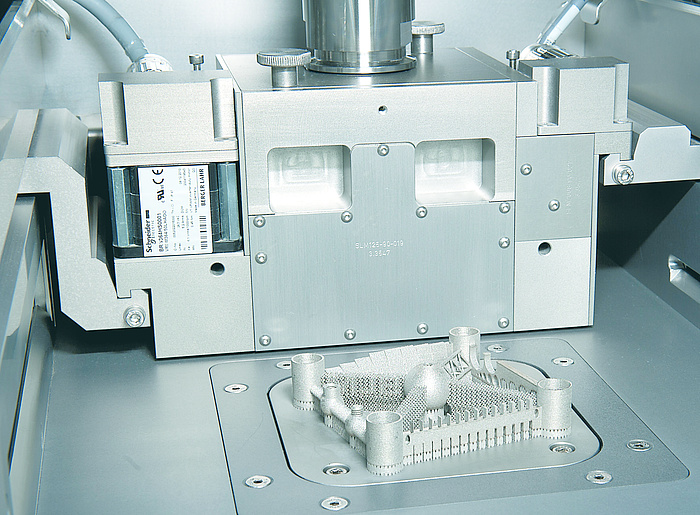
Additive manufacturing
Until a few years ago the operational capability of these technologies belonged clearly and solely to the realm of rapid prototyping. They were technologically ingenious but too slow and too expensive, for production at a bigger scale. But things have changed. Fast growing composition rates and an increasing number of producers of the relevant machinery are inexorably repositioning additive manufacturing from being a tool to the field of application of real production. The complexity of work preparation is decreasing; there is now little need for purchasing and using special tools and fixtures, and multiple joining operations (glueing, riveting, screwing, etc.) are becoming obsolete. Last but not least, a tremendous reduction in warehousing and material disposition is leading to the important savings that justify an investment for this new form of manufacturing. The objection that parts made by additive manufacturing do not comply with high standards in safety and stability requirements or cannot be used for series production can be countered simply and exemplarily by the fact that Airbus produces brackets for its hydraulic tanks via 3D printing, and also Boeing has gained approval from the American Federal Aviation Administration to produce the injection nozzles of its turbines using additive manufacturing.smartfactory@tugraz
Advanced Manufacturing does not only comprise the presentation and mastering of single technologies but promotes the formation of integrated, transparent and especially fast working process chains by means of the current possibilities of digitalization which can integrate downstream and upstream process steps beyond the company (suppliers and customers). This is turning Advanced Manufacturing – as an element of a versatile Production 4.0 philosophy – into a very valuable and promising manufacturing strategy also from a customer perspective. For the purposes of research and demonstration of these revolutionary new capabilities, Graz University of Technology is currently establishing a 250 square meter pilot factory which will be run under the name smartfactory@tugraz. The installation of cutting-edge machinery and an appropriate IT infrastructure will show intelligent linkages, possible interaction and flexible programming of a modern manufacturing system. A further goal in this smart factory is to manufacture products or components from the real world of industry. Thus the smartfactory@tugraz will not only be a place of research but also a meeting point for members of other institutes, for students and industrial partners of the University.
Kontakt
Univ.-Prof. Dipl.-Ing. Dr.techn.
Institute of Production Engineering
Kopernikusgasse 24/I
8010 Graz, Austria
Phone: +43 316 873 7674
<link int-link-mail window for sending>rudolf.pichler@tugraz.at