Temperature measurement for Smart Production
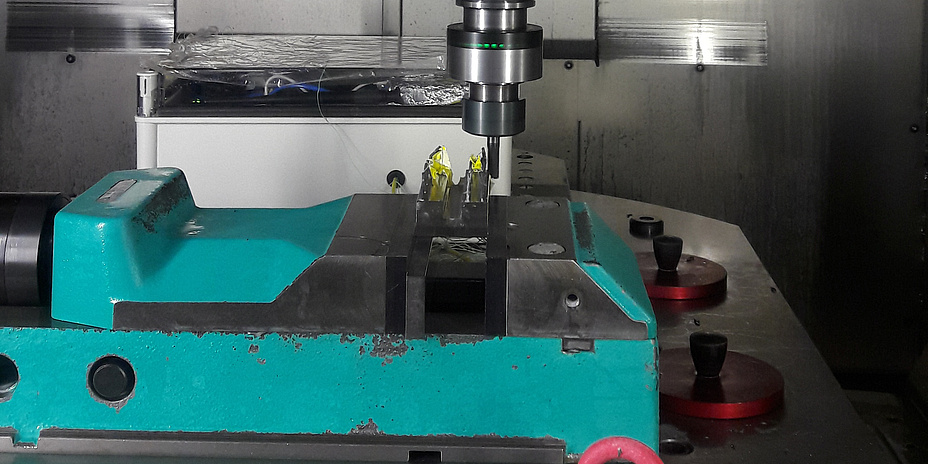
“What is sensational about our project can be found hidden away in this rather inconspicuous chart,” says Franz Haas from the Institute of Production Engineering as he points to a diagram reproducing a saw-toothed temperature progression for the period of a tenth of a second (Figure 2). The cutting temperature resulting from milling a titanium alloy (Ti64) was measured on the cutting edge. The sampling frequency necessary for this amounts to 20 kHz and was only possible due to a piece of hardware developed by the Institute. In other words: 20,000 temperature values are captured and processed in 1 second. The method developed at TU Graz is thus twelve times more accurate than the best system currently available on the market for process data acquisition during milling, which has maximum sampling rate of 1.6 kHz
The cutting temperature gradient at the cutting edge while milling a titanium alloy. © Institute of Production Engineering
It is extremely important to know the temperature development of some materials during processing: for instance, in titanium alloys, which are used in lightweight construction, and also in carbon-fibre reinforced polymers (CFRP). CRFP materials frequently find application in the aerospace industry due to the fact that they offer maximum stiffness at minimum weight. One risk involved in their processing is that the high temperatures can damage the matrix, thus destroying the material-composite structure. This can lead to sudden fragmentation when subjected to stress at a later stage or to a fracture of the included materials as a result of a delamination of the structure. For this reason it is extremely important not to exceed the material-dependent temperature limits during milling. “Whereas measurements have returned an average value of the occurring temperature fluctuations, our high-resolution method also allows temperature peaks during processing to be recognised even at the individual teeth of the tool,” explains Franz Haas.
Darmstadt, Reutte, Leoben, Graz
The name of the research project CHIP stands for Competence Through Highly Intelligent Production with a unique Temperature Sensor in Milling Tools”. “A chip is of course a waste product from milling, but the name of the project also hints at the electronic we’re developing,” says Franz Haas. TU Graz is working on the CHIP project together with the Institute of Production Management, Technology and Machine Tools at TU Darmstadt and the K2-centre Materials Center Leoben. The operator and consortium manager of the Austrian Research Promotion Agency (FFG) funded project is the Ceratizit Group. The affiliated company of the Tyrolean Plansee AG specialises in cutting tools and hard-metal solutions for precision processing of a wide range of materials..
“Collaboration with the company and the research partners is running very well,” reports Haas. The project team meets up four times a year to exchange preliminary results and to talk about the next steps. Meetings take place alternately in Darmstadt, Reutte, Leoben and Graz. “The last meeting took place in Reutte. The meetings are always very productive, and take place on a personal level.”
Data volume and practical knowledge
For Franz Haas, exchanging practical knowledge on a personal level is at risk from missing out against the background of Big Data. It’s surprising to hear a technology professor talk like this, someone at whose institute a measuring method is being improved, when he says as an aside: “In the field of production processes there is a lot of know-how which is not written down. This practical knowledge, this knowledge which you can’t look up, is something very valuable that should be understood as an essential treasure for every company and made digitally useful.”
A test using metal shavings, the waste product during milling. © Institute of Production Engineering
But back to the CHIP project. The experimental set-up, the development of the prototype and especially the attachment of only 0.25mm¬thick thermoelements in specially prefabricated milling tools were mechatronically very challenging. The experiments were led by the young Chinese technologist Wenqi Liu, a mechatronics graduate from Johannes Kepler University Linz, who has been working on her doctoral thesis at TU Graz in the context of the project for almost two years. In Haas’s view, the innovation of CHIP lies in its interdisciplinary approach: namely, in the cross¬over between mechanics, electronics and software. “Through better electronics, measurement and control technology, a huge improvement potential is opening up with respect to applications in production technology,” says the production technology professor. “The interim results of the present project will allow us to design milling and other production processes more efficiently in the spirit of machine learning. This is particularly important for quality assurance when you’re processing temperature¬sensitive materials. The challenge now is to develop an algorithm by which one can filter results out of the mass of data which can lead to concrete improvements of the tool, in machine and product quality.”
This research project is attributed to the Field of Expertise „Mobility & Production“, one of TU Graz' five strategic areas of research.
Visit Planet research or more research related news.
Kontakt
Franz HAAS
Univ.-Prof. Dipl.-Ing. Dr.techn.
Institute of Production Engineering
Kopernikusgasse 24/I
8010 Graz
Phone: +43 316 873 7170
franz.haas @tugraz.at