The EU’s climate targets aim high and don’t let up for passenger vehicles. In 2020 new cars will only be allowed to emit on average 95 grams of
CO2 per kilometre; in 2015 the
CO2 emission of a new car was about 120 grams. These drastic reduction measures are justified by the fact that passenger vehicles presently count among the main
CO2 polluters. The current most promising approach to
CO2 reduction lies in the electrification of the drive train, either in the form of purely electrically powered vehicles or in hybrid vehicles, which are propelled by a combination of combustion engine and electric motor. Vehicle manufacturers have two possibilities: either to develop completely new vehicles or to adapt existing models. In the design of the electric drive, various demands on performance, energy efficiency, space and costs – which influence each other in a complex way – have to be taken into account.
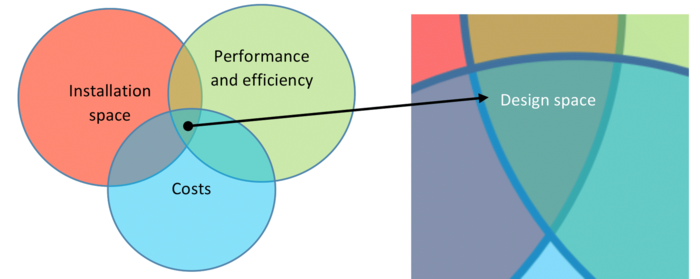
In designing electric drives, aspects from various domains have to be taken into account.
And it is exactly this challenge that Martin Hofstetter from the Institute of Automotive Engineering at TU Graz has taken on. In his doctoral thesis he’s developing a computer-aided design process which is meant to optimally size the electric powertrain for hybrid and electric cars. Performance, energy efficiency, installation space limitations of the respective car model and resulting costs are considered. "At present the optimisation potential for electric drives cannot be completely exhausted through conventional methods of calculation. In the future, the new method should also reduce development time, which will in turn lower development costs and vehicle costs," elaborates Martin Hofstetter.
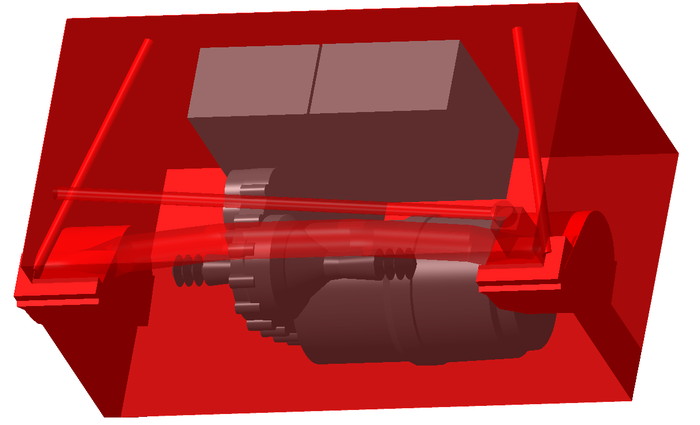
The digital installation space model (red) illustrates geometrical restrictions resulting from the vehicle design. On the basis of this, solutions for the electric motor, gearbox and power electronics are calculated (grey).
Crucial price factor
Electric and hybrid cars are not just one jump ahead of classical petrol or diesel vehicles with respect to pollutant emissions. The electric drive has a positive impact on acceleration behaviour and noise generation. Higher acquisition costs of electric and hybrid cars are, however, largely responsible for the fact that consumers do not buy vehicles with alternative drives more often.
Faster to the best solution
The software developed by Martin Hofstetter is based on a library of already available component technologies – in other words, different electric motors, gearbox models and variants of power electronics. "On the basis of requirements, the software automatically performs an initial selection of suitable parts which can be weighed up against each other in the next step within the overall system regarding space requirements, power and costs," explains Martin Hofstetter. "This enables us to compare a number of solutions side by side – each with their respective technically related advantages and disadvantages – and thus find the best combination of parts."
The "tool" designed by Martin Hofstetter is meant to offer support in particular in the early project phase of vehicle development, when it is still not clear which technical concept can best live up to demands. By means of this computer support, the best concept for the design of the electric powertrain can be worked out faster, thus allowing the engineering team to concentrate on the technically demanding detailed solutions.
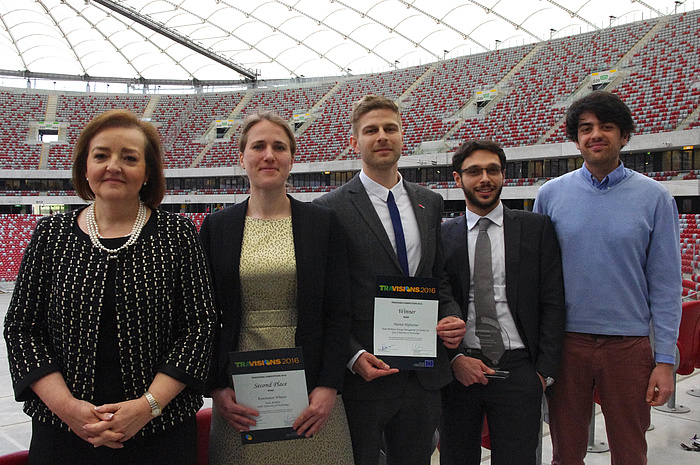
For his master’s thesis, Martin Hofstetter (centre) won the Road Award of the Travisions Contest 2016, in which 130 students from 14 EU countries took part. The annual contest is supported by the Horizon 2020 EU Framework Programme to reward innovative research projects for the future of the European transport industry.
This research project is anchored in the Field of Expertise "Mobility & Production", one of five research foci of TU Graz.
Martin HOFSTETTER
Institute of Automotive Engineering
Inffeldgasse 11/II
8010 Graz
Phone: +43 316 873 35285
<link int-link-mail window for sending>martin.hofstetter@tugraz.at
<link http: www.tugraz.at institute ftg _blank int-link-external external link in new>
www.tugraz.at/institute/ftg