Plastics as Heat Managers for High-Tech Products
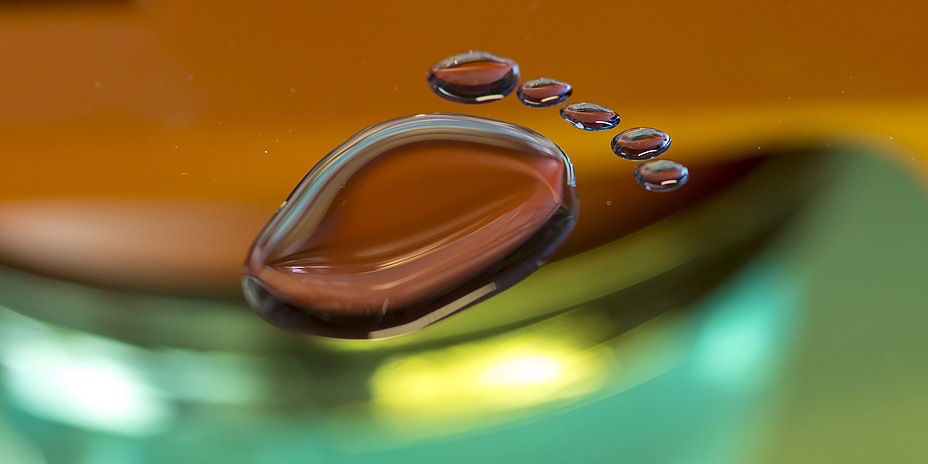
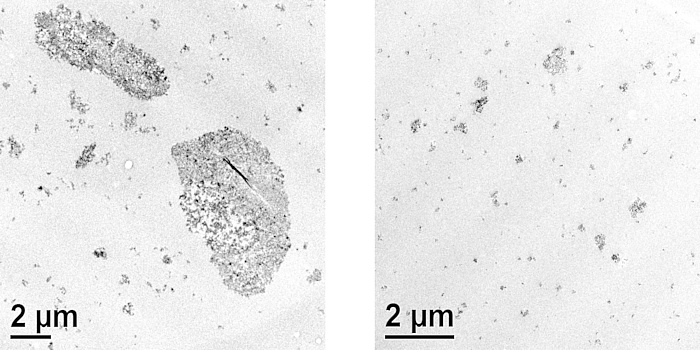
High-perfomance plastics in heat management
The chemist at the Polymer Competence Center Leoben (PCCL) and the Institute for Chemistry and Technology of Materials at TU Graz heads the interdisciplinary K-project “PolyTherm – Polymer Composites for Thermally Demanding Applications”. Together with researchers from chemistry, materials science, plastics and high-voltage engineering as well as industry partners, several objectives are being pursued in the project. “On the one hand, we want to analyse temperature developments and their associated burden on the materials in power electronics systems in simulations. These findings will help us to accurately assess the service life and reliability of electronic components. On the other hand, on the basis of these analyses we will be developing suitable polymers and polymer composites with improved thermo-mechanical properties which show the best performance in use,” says Frank Wiesbrock.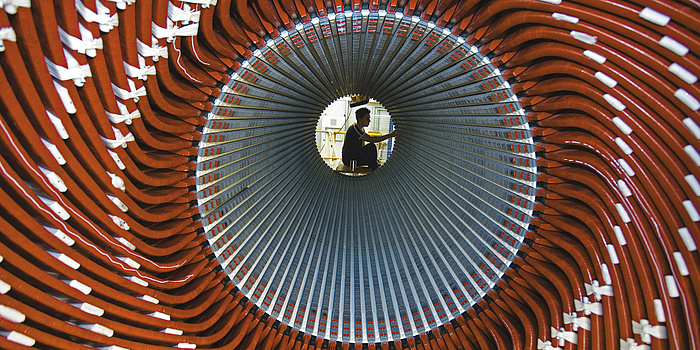
Polymers from renewable raw materials
Special attention will be given to environmental sustainability through the innovative material concepts developed in PolyTherm. “We are developing and testing environmentally friendly polymers with their origin in nature as an alternative to mineral oil synthetic resins. We have already been able to show that rapeseed oil is suitable as a good basis for producing innovative insulating plastics,” says Frank Wiesbrock. The developments are also important with regard to employee protection. This is due to the fact that some of the classical, mineral oil based epoxy resins contain components which may pose health risks in high concentrations. For this reason development from alternative materials is also a long-term aim.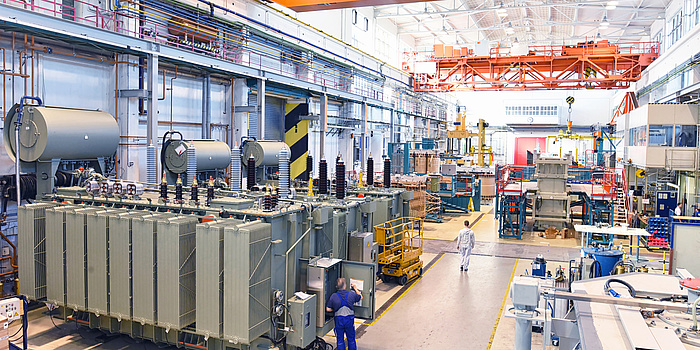
Interdisciplinary research alliance
In the framework of the COMET programme of the Austrian Research Promotion Agency using funds from the Ministry for Science, Research and Economy and the State of Styria, a budget of six million euros is available for the four-year PolyTherm project which started at the beginning of 2017. On board the project are institutes of five universities among which are TU Graz’s <link https: www.tugraz.at institute ictm home _blank int-link-external external link in new>Institute for Chemistry and Technology of Materials, the <link https: www.tugraz.at en institute hspt home _blank int-link-external external link in new>Institute of High-Voltage Engineering and System Management which among other things will carry out load tests and dielectric characterisations, and the <link https: www.ac.tugraz.at index.php wbindex _blank int-link-external external link in new>Institute of Inorganic Chemistry. Six partner companies from the microelectronics and high-voltage engineering sector will augment the competence network.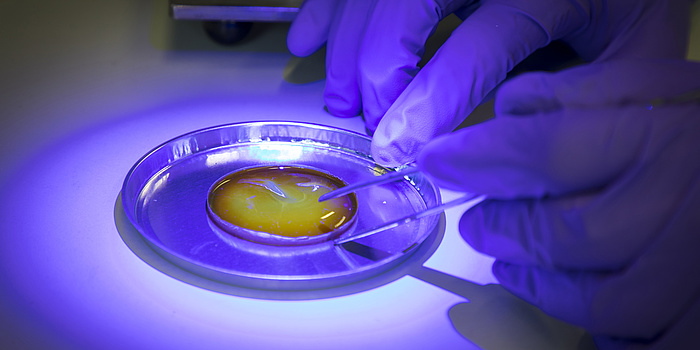
Polymere mit nanoskalierten FüllstoffenPolymers with nanoscale fillers
Plastics by definition are not good heat conductors and, in general, only have moderate temperature stability. The results which will be obtained from PolyTherm should change all that. A temperature stability up to 180 degrees Celsius is being sought in the new polymers (insulation class H). In comparison, the polymers currently being used have a general temperature stability up to 155 degrees Celsius (insulation class F). The researchers want to achieve this by attaching inorganic, nanoscale fillers onto the polymers. “By combining the nanoparticles with the polymers in a controlled way, we can create new composite materials with certain properties that we can ‘fine tune’,” explains Frank Wiesbrock.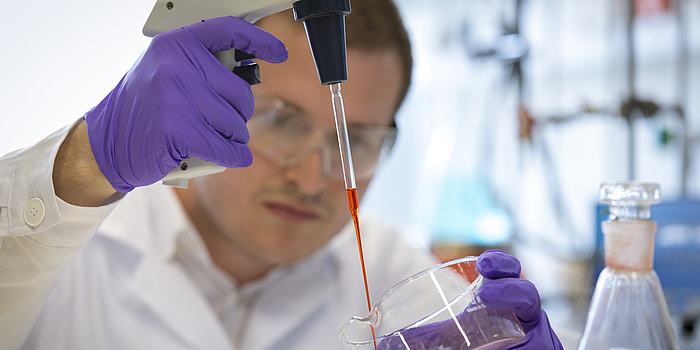
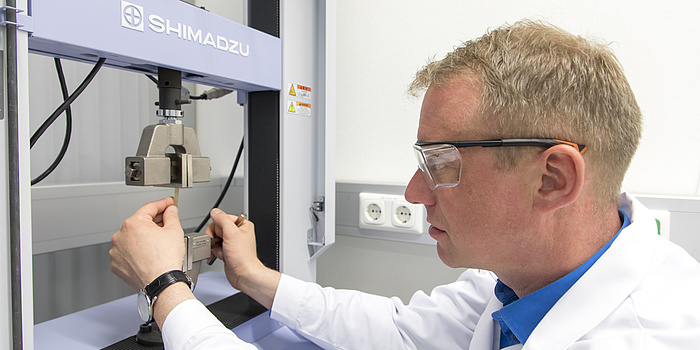
Preventing tears during expansion and hardening
Another challenge to the researchers is thermal expansion during heat build-up: this can become a problem when layers of different materials are joined. “On the one hand, the bond between metals and polymers becomes worse when they expand differently due to increasing temperature. On the other hand, polymers can develop tears or hardening, something which has a negative effect on the insulation properties,” explains Frank Wiesbrock. For this reason, the researchers are trying to design the polymers in such a way that a part of the molecular chain increases its volume, while the other part shrinks. In this way the volume of the plastic can remain largely constant even during hardening.Tailor-made plastic building blocks
The evaluation of alternative production technologies has been planned in the PolyTherm project. “Polymers and polymer composites have outstanding material properties for high-voltage engineering. But because each part has to be adapted to the available environment, even these smallest elements are subject to highly specialised tailor-made solutions. Polymer components are still manufactured according to conventional methods which are generally cost intensive,” says Frank Wiesbrock. But in the future, cheaper and faster processes could be relied on, though currently only a small number of polymers are suitable. “We want to change this by evaluating the uses of certain additives,” continues Frank Wiesbrock. From a regional point of view, PolyTherm enhances the visibility of the newly established Silicon Alps Cluster, which combines Austrian players from science, economy and the public sector and should open up unique potentials in microelectronics and electrical engineeringThis research project is attributed to the Fields of Expertise <link https: www.tugraz.at forschung forschungsschwerpunkte-5-fields-of-expertise advanced-materials-science ueberblick-advanced-materials-science _blank int-link-external external link in new>„Advanced Materials Science“ , one of TU Graz' five strategic areas of research.
Kontakt
Priv.-Doz. Dipl.-Chem.Univ. Dr.rer.nat.
Institut of Chemistry and Technology os Materials
Stremayrgasse 9
8010 Graz
Phone: +43 316 32283
<link int-link-mail window for sending>f.wiesbrock@tugraz.at
<link http: ictm.tugraz.at _blank int-link-external external link in new>ictm.tugraz.at