Optimised Parcel Logistics through Virtual Models
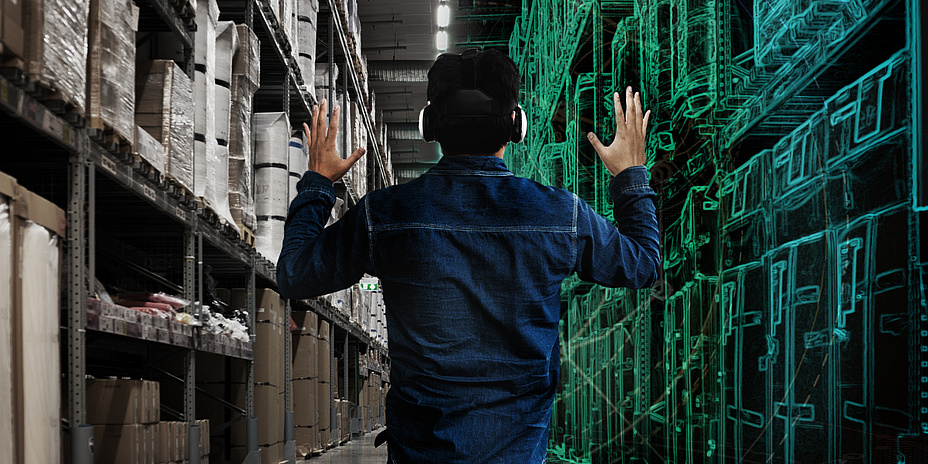
Parcel hubs are quite mysterious entities for outsiders. Parcels are delivered at one point and travel on in the right direction after a sorting process – but most people don’t know exactly how this works. Of course, there are pictures and videos of conveyor belts, parcel chutes, scanners, sorting staff and everything else that goes with it. It’s difficult even for experts to get an overview of what happens when, where and how, and what influence this has on the subsequent workflow. On the other hand, this means that there is still a lot of potential for optimisation to make processes not only faster and more efficient, but also more reliable, so that parcels reach their recipients undisturbed even more often than before.
Human factor difficult to simulate
The Institute of Logistics Engineering at Graz University of Technology (TU Graz) is developing 3D simulation models of parcel hubs in order to tap into this potential and at the same time support staff by making improvements. “We can use these models to design new facilities or optimise existing ones,” says Harald Steinkellner from the Institute of Logistics Engineering. “We want to use it to make processes more efficient, for example by positioning conveyor belts and parcel chutes in a targeted manner. But it can also be used to improve picking and packing processes or train the team. We can also experiment with layouts and see how many staff are needed in certain areas or what happens if something goes wrong.”
For this endeavour to really succeed, it is essential that the simulations accurately reflect the real world, i.e. that the computer model corresponds to a digital twin of the original. With the facilities and technical systems, this is usually achieved as desired, but human behaviour remains a limiting factor, as the individuality of people poses particular challenges in the context of modelling. The researchers are therefore constantly fine-tuning their models based on new data in order to increase their accuracy. They take into account factors such as the speed at which people work, the mistakes they make, fatigue and distractions.
Flexible packaging simulated with physical accuracy
For a long time, it was also difficult to predict the physical behaviour of consignments that deform easily, such as polybags and parcels made of thick paper. To this end, the Institute of Logistics Engineering has developed a new method in a separate project that allows the behaviour of flexible parcels to be simulated with physical precision. However, it has only been possible to simulate the behaviour of individual flexible consignments up to now. A new project is currently looking into the simulation of several of these consignments and their interactions with each other. Due to the numerous physical influences, this is definitely a challenge.
And why all this? On the one hand, to improve efficiency in the parcel hubs, as already mentioned. This means that operators can receive a computer model of their hubs within a few weeks and use it to plan improvements to the layout. In addition to the ideal positioning of technical components, those responsible can also consider the dynamics of the employees. They can simulate how many employees they deploy and where, and create efficient shift plans and adjust them in real time if people are absent.
Better understanding of their own contribution
At the same time, the simulation can also provide the employees themselves with a better understanding of their work. In this way, they learn to understand what part their work plays in the overall process. This gives them a new perspective on the contribution of their actions to the overall result, which they lack in their day-to-day work.
Despite these many possibilities, work on these simulation models is far from complete. Harald Steinkellner predicts that AI and machine learning in particular will be integrated even more in the future in order to predict trends and optimise systems in real time. “Decisions are becoming increasingly data-driven, i.e., they are based on sound analyses of large volumes of data, which are evaluated using AI, for example, in order to identify patterns, create forecasts and derive well-founded recommendations for action,” says Harald Steinkellner. “We will use new technologies to detect problems before they even arise. We will move through the hub with VR glasses and can see directly what impact our decisions have. And we will map the entire delivery system virtually, not just the hub. We then have a model for the entire supply chain, from ordering to delivery at the front door. This enables us to find bottlenecks and optimise the entire system in terms of efficiency and sustainability.
This article is part of the TU Graz Dossier "Logistics - Getting everything from A to B“. You can find other dossiers at www.tugraz.at/go/dossiers.
Kontakt
Harald STEINKELLNER
Dipl.-Ing. BSc
TU Graz | Institute of Logistics Engineering
Phone: +43 316 873 7331
harald.steinkellner @tugraz.at