The research and test facility set up by ABB AG Austria is designed for wet and dry machining of large components. Both hard and soft materials can be machined by grinding and milling.
The individual components of the plant are:
ABB machining robot
NOMOTEC linear axis
PDS machining spindles
In addition, the system has an automatic tool change system as well as the force sensor control "Force Control". Furthermore, a powerful extraction system is available in the machining cell.
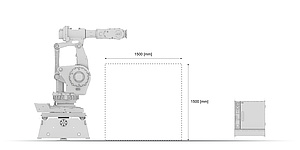
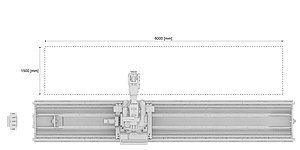
Depending on the material, tool and workpiece geometry, machining accuracies of less than +/- 0.2 [mm] can be achieved in a machining area of 6000 x 1200 x 1200 [mm].
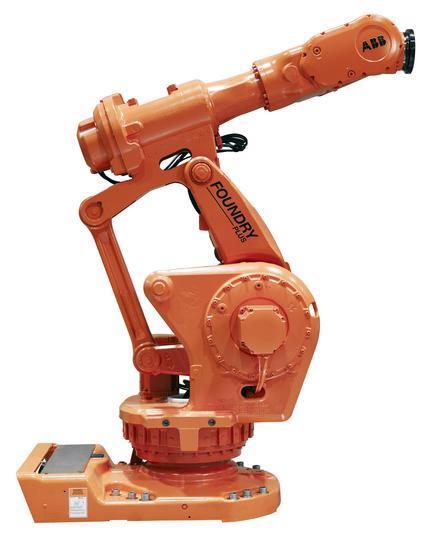
Unlike most existing systems, the system described here is equipped with a precision linear axis, which was designed and built by Nomotec. With a dead weight of 7.0 t, a maximum permissible payload of 2.2 t and a total length of 7400 mm, it offers the possibility of moving the robot over a length of 6000 mm.
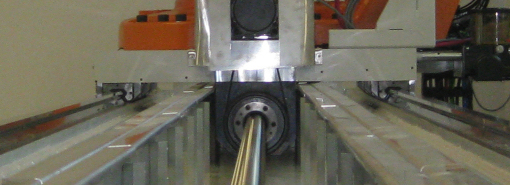
The moving base plate, which weighs around 800 kilograms and on which the machining robot is mounted, is supported by linear ball bearings and is driven by a ø 70 millimetre ball screw. The drive of the axis is implemented as a seventh axis in the robot control.